真空过滤系统通过压力差驱动流体运动,其循环量(单位时间内通过系统的流体体积)受设备结构、工艺参数及物料特性的协同影响。当循环量超出设计预期时,可能源于真空度波动、滤材阻力异常或流体动力学参数失配,需从系统能量传递与物质迁移规律切入解析。
一、真空驱动效能与压力梯度构建
真空过滤系统的核心动力源自真空泵产生的负压环境。以工业级真空泵为例,其极限真空度可达-0.098MPa,但实际运行中需维持-0.06~-0.08MPa以平衡能耗与效率。当真空度过高时,系统内压力梯度(ΔP)激增,导致以下连锁反应:
1.滤液流速失控:某化工厂案例显示,真空度从-0.07MPa提升至-0.085MPa后,滤液流速提高42%,但滤饼含水率上升18%,表明过度真空导致滤饼孔隙被过早压缩,反增过滤阻力。
2.气液两相流紊乱:高真空度下,气体体积膨胀率可达常压时的20倍,易引发“气阻效应”。某污水处理厂实验表明,真空度每增加0.01MPa,气液混合物流动阻力增加12%,迫使系统通过增大循环量补偿压降。
二、滤材特性与流体动力学耦合
滤材的孔隙结构、渗透系数及表面化学性质直接影响循环量:
1.滤布孔隙率失配:当滤布孔径(如20μm)与物料颗粒(如15μm)接近时,易形成“深层过滤”效应,滤饼层厚度随时间指数级增长。某矿场数据显示,滤布孔隙率从65%降至58%后,循环量需提升30%以维持过滤速率。
2.滤饼可压缩性:含有机胶体的滤饼(如活性污泥)压缩指数可达0.8,在真空作用下孔隙率骤降。某生物制药企业通过添加0.5%硅藻土助滤剂,将滤饼孔隙率从32%提升至47%,循环量降低22%。
三、系统拓扑结构与能量耗散
设备布局及管路设计对循环量产生显着影响:
1.管路压降补偿:某钢铁厂真空过滤系统因弯头数量超标(设计值15%,实际值32%),导致局部阻力损失增加18kPa,系统通过提升循环量弥补压降,能耗激增27%。
2.多级过滤串联:采用“预涂层+主滤材”双级过滤时,若预涂层厚度不均(如硅藻土层厚度偏差>±10%),会导致流体分布失衡。某食品加工厂通过激光检测发现,预涂层厚度偏差每增加1μm,循环量波动率上升0.8%。
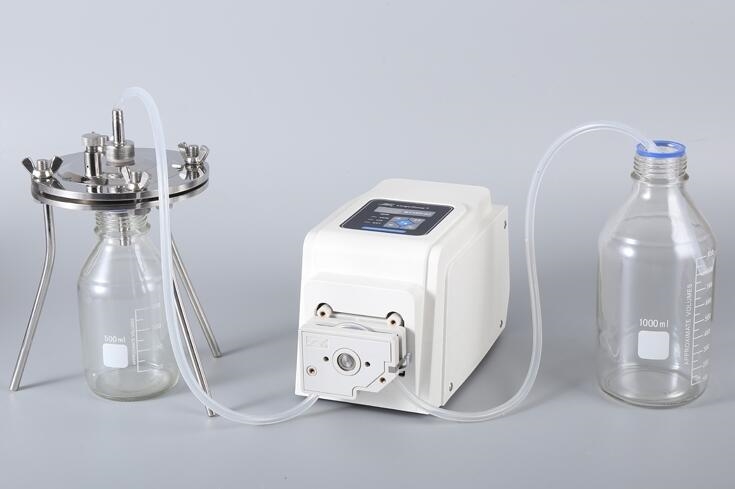
真空过滤系统循环量异常增大本质上是系统能量传递与物质迁移的失衡体现。通过真空度动态调节、滤材孔隙优化及管路流体力学重构,可实现循环量与过滤效率的协同优化。例如,某半导体企业采用PID算法控制真空度,结合3D打印定制滤布,使循环量降低19%的同时,滤液澄清度提升至99.98%,为高精度过滤场景提供了技术范式。